Nylon is one of the most used polymers for fibre manufacturing for several applications, including refractory, sealants, casting, and plastics. We have been working with various industries for years that use nylon due to its beneficial properties.
In this blog, we specifically look at how nylon fibres are used to enhance strength and reinforce plastics, looking at our findings in a recent case study that we carried out.
What Are Nylon Fibres?
Nylon is a synthetic, silk-like thermoplastic that can be melted into fibres, films, or shapes. Thermoplastics can be heated to their highest melting point, cooled, and reheated without suffering significant degradation. Rather than burning, thermoplastics, like nylon, turn into liquid, allowing them to be easily injection moulded as well as recycled. Common thermoplastic polymers are polyester, polyvinyl chloride, as well as thermoset epoxy and vinylester.

Nylon is a name for a family of synthetic polymers (also known as aliphatic or semi-aromatic polyamides) made from polyamide molecules.
The first nylon (polyamide) material was developed in the 1930s and became quickly attractive due to its high strain to failure, low density, and durability. Nylon was produced by an American chemist who worked at the DuPont research facility. Nylon particularly became popular during the second world war when there was a short supply of other natural materials, including silk, rubber, and latex.
How is Nylon Made?
Nylon production predominantly falls into two categories. The first is the reaction of monomers with amine (NH2) groups reacting with carboxylic acid (COOH). The other is the reaction of diamine (a molecule with two NH2 groups) and dicarboxylic acid (which has two COOH groups).
Typically, nylon is made through the distillation of hydrocarbon fuels and are sometimes combined with other catalysts to produce plastics via polycondensation or polymerization. Nylon can also be made from biomass to ensure it results in a more biodegradable material.
What Are Reinforced Plastics?
Reinforced plastics (or plastic composites/composites) are just plastics whose characteristics have been altered or enhanced by adding other materials. RPs are essentially tailor-made materials that provide manufacturers with engineered flex to achieve different shapes, properties, and other enhancements.
Any synthetic plastic material that’s composed of polyamides with high molecular weight is normally manufactured as a fibre. The most common variant for engineering applications is Nylon 6/6 as it can be extruded and is a suitable plastic for injection moulding and 3D printing. Other variants include Nylon 6, Nylon 66, and Nylon 6/66. The numbers indicate how many carbon atoms are between the acid and amine groups. At Goonvean Fibres, we use Nylon 6/6 to achieve precision cuts.
Why is Nylon Used So Often?
Nylon is widely used because of its excellent mechanical properties. It can be easily melted into filaments, fibres, films, and sheet stock, making it ideal for a wide range of manufacturing applications. Its adaptability, diversity, and high performance make it an excellent choice for manufacturing products that could result in a lot of wear, including chain guides, gears, bearings, compressor vanes, and impellers.
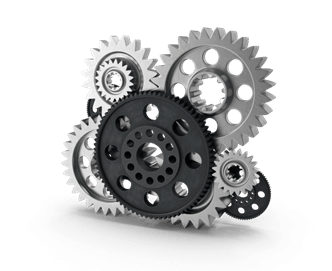
Nylon is also used in clothing, sports supplies, food packaging, and automotive accessories.
Plastics are usually reinforced with nylon to improve mechanical properties, making the plastics stronger and more elastic and benefitting manufacturers with the ability to create different properties, environments, and shapes for various applications.
The Benefits of Adding Nylon to Plastic Formulations
Nylon has a wide range of positive characteristics that make it an enduringly popular material, including:
- Hardwearing and durable
- Resistant against sun damage and sunlight
- Soft to touch
- High melting point
- Colourfast
- Abrasion resistant
- High melting point
- Easy to dye
- High elasticity and elasticity recovery
- Can be combined with liquids and gels
- Resistant against insects, fungi, mould, animals, mildew, and rot
- Resistant against chemicals
Nylon is also a highly cost-effective alternative to carbon fibre and is much safer to handle than glass fibre.
Goonvean Fibres added our Milled Nylon Fibre to plastic formulations to improve tear resistance and internal strength in a recent study that we carried out, specifically for automotive applications. The benefits we saw were:
Fibre Property | Benefits in Plastics |
Light-weight reinforcement | Improved strength to weight ratio of parts lead to fuel efficiency in automotive applications |
Hardness (Hardest synthetic fibre) | Improved abrasion resistance for increased lifetime of parts |
Uniform dispersion of fibres | Effective stress transfer throughout the matrix through the even distribution of fibre reinforcement |
Orientation in the matrix | Can provide strength properties in the direction of a primary load |
- The strength improved to the weight ratio of parts lead to fuel efficiency due to the nylon lightweight reinforcement property.
- Improved abrasion resistance for increased lifetime parts thanks to the nylon’s hardness.
- Effective stress transfer throughout the matrix through the even distribution of fibre reinforcement due to the nylon’s uniform dispersion.
- Greater strength properties in the direction of a primary load due to the nylon’s orientation in the matrix.
The results show that our nylon is highly effective at enhancing and reinforcing plastics. If you’re interested in finding out more about our plastic reinforcement solutions using nylon fibres, why not contact us? We are happy to tailor to your specific needs and requirements.