Goonvean
POLYETHYLENE
FIBRE


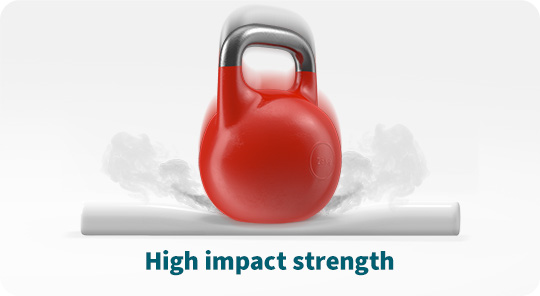
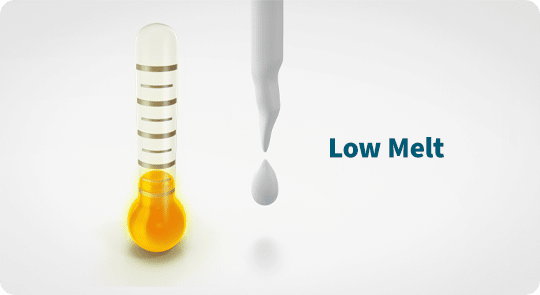
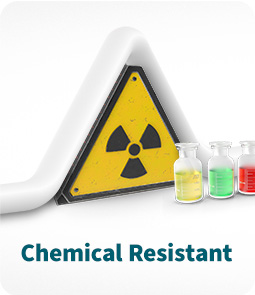

An Excellent Electrical Insulator
Polyethylene fibres (polythene or PE) are fatigue and wear-resistant plastics used for a wide range of manufacturing techniques to achieve flexibility, high ductility, and resistance against chemicals and water. PE is commonly used to manufacture marine components, piping systems and liquid dispensing equipment. The fibre is excellent at improving matrix adhesion when melted.
PE is not toxic and is food safety approved, making the fibres suitable for food processing parts and medical equipment.
Quality matters, so at Goonvean Fibres, we’ve designed Precision-Cut and Milled Flock Polyethylene fibres to tailor to specific needs and requirements with additional values such as zero fusion, improved flow characteristics, shorter cut lengths, and lower customer production costs.
Available in a range of sizes.
Standard Fibre Details
PE has many beneficial characteristics, including low friction, electrical insulation, chemical and solvent resistance, zero water absorption, flexibility, impact strength and resistance, and resistance against fatigue. Our PE fibres are second to none, so rest assured you will receive the finest quality.
Technical Fibre Details
Polyethylene is a thermoplastic polymer with a variable crystalline structure. PE can be used for a vast range of applications in manufacturing. It’s the most used plastic worldwide for products such as clear food wraps, shopping bags, and fuel tanks.
PE is made from the polymerization of ethylene monomer, and its chemical formula is (C2H4)n.
Polyethylene (PE3)
Characteristic | Unit | Specification | Method |
Moisture Content | % | 0.0 -0.1 | WI 107 |
Melting Point | °C | 132 – 135 | WI 309 |
Density | g/cm³ | 0.90 – 0.91 | WI 300 |
Dry Elongation at Break | % | 50 – 70 | WI 311 |
Polyethylene Powder (HMPE95A, HMPE125A, HMPE95A)
Characteristic | Unit | Specification | Method |
Moisture Content | % | 0.0 – 0.1 | WI 107 |
Melting Point | °C | 124 – 136 | WI 309 |
Density | g/cm3 | 0.95 | WI 300 |
Melt Flow | 190 °C, 2.16 kg | 4 – 16 | N/A |
Dry Elongation at Break | % | >550 | WI 311 |
Tensile Strength at break | MPa | 31 | N/A |
Polyethylene Powder (HMPE35A)
Characteristic | Unit | Specification | Method |
Moisture Content | % | 0.0 – 0.1 | WI 107 |
Melting Point | °C | 98 – 113 | WI 309 |
Density | g/cm3 | 0.91 – 0.92 | WI 300 |
Melt Flow | 190 °C, 2.16 kg | 48 – 92 | N/A |
Dry Elongation at Break | % | 220 | WI 311 |
Tensile Strength at break | MPa | 10 | N/A |
Polyethylene Powder (HMPE400A)
Characteristic | Unit | Specification | Method |
Moisture Content | % | 0.0 – 0.1 | WI 107 |
Melting Point | °C | 98 – 113 | WI 309 |
Density | g/cm3 | 0.91 – 0.92 | WI 300 |
Melt Flow | 190 °C, 2.16 kg | 48 – 92 | N/A |
Dry Elongation at Break | % | 220 | WI 311 |
Tensile Strength at break | MPa | 10 | N/A |
Polyethylene (HMPE500A)
Characteristic | Unit | Specification | Method |
Moisture Content | % | 0.0 – 0.1 | WI 107 |
Melting Point | °C | 98 – 113 | WI 309 |
Density | g/cm3 | 0.91 – 0.92 | WI 300 |
Melt Flow | 190 °C, 2.16 kg | 48 – 92 | N/A |
Dry Elongation at Break | % | 220 | WI 311 |
Tensile Strength at break | MPa | 10 | N/A |
To find out more, get in touch. We are happy to help you incorporate our fibres into your products, as well as discuss any bespoke requirements.